Want to know about the Kaizen method and how it can help you take your business to the next level? You have come to the right place!
Do you know what makes life interesting and worthwhile? The motivation to be better than you were the day before. By continually improving every aspect of our lives- be it personal or professional, we can strive forward and be the best versions of ourselves that we always aspire to be.\
Our businesses operate in the same way. Each day we have a desire to be better, produce a better quality product, deliver faster, generate more users, drive more traffic, increase social media followers, provide the best experience to our customers, etc.
The way to continually improve in the world of business is to make improvement a part of your daily routine. No matter how big or small the changes are, as long as they reap positive benefits to our business, they should be implemented.
Imagine if everyone at your company was focused on improving various aspects of your business so that collectively your business operates better with each passing day.
This employee focus on continuous improvement in business processes is what Toyota calls Kaizen.
Kaizen is a lean manufacturing technique that aims to improve process efficiency, quality, reduce waste, increase productivity, safety, and workplace culture.
Kaizen is about achieving improvements by taking small steps instead of drastic, radical changes. These small increments lead to big improvements over time, which is why Kaizen has been the go-to method for process improvement.
A Brief History Of Kaizen
Kaizen comes from two Japanese words: Kai (improvement) and Zen (good), which roughly translates to “continuous improvement”.
In business, Kaizen refers to activities that continually improve all functions and involve all employees from the CEO to the assembly line workers. The Kaizen methodology first came into existence during the effort to rebuild Japan after World War II.
At the time, several U.S. business consultants worked with Japanese companies, especially Toyota to improve manufacturing. Their joint efforts, with guidance from American management consultant, W. Edwards Deming, resulted in the development of several new management techniques, one of which was Kaizen.
Since Kaizen involves small steps and incremental changes, it is a low-risk and inexpensive approach. As a result, Kaizen encourages workers to experiment and try out new ideas without the fear of losing out on large capital investments.
Kaizen is not just about process improvement or waste management, its a managerial mindset that involves every worker in the organization, trying their best to commit to one small improvement on a daily basis.
Read more: What is Workplace Collaboration & How To Do It Right!
The 10 Principles of Kaizen
There are a few basic principles that anyone implementing Kaizen in their personal or professional lives should adhere to. These are:
- Let go of assumptions
- Be proactive
- Challenge the status quo
- Let go of perfectionism and take an attitude of iterative, adaptive change
- Look for solutions
- Create an environment in which everyone feels empowered to contribute
- Don’t accept the obvious issue; instead, ask “why” five times to get to the root cause
- Involve multiple people in the process and ask for their opinions
- Use creativity to find low-cost, small improvements
- Never stop improving.
Why You Must Implement Kaizen?
By properly implementing Kaizen at your workplace, you can achieve positive results in various aspects of your business.
Kaizen is not just about process improvement or waste management, its a managerial mindset that involves every worker in the organization, trying their best to commit to one small improvement on a daily basis. There are thus, many advantages to implementing Kaizen at your organization-
1. Increases Teamwork
As mentioned before, implementing Kaizen methodology is not supposed to be a one-person job. Every person in the organization, from line workers to the CEO- everyone is involved in trying to find out small errors and gradually improving the processes. This leads to improved teamwork amongst the members of the organization.
Read more: 50 Best Team Building Activities For Collaboration
2. Utilization of Resources
Kaizen is all about the utilization of existing resources to make incremental changes. Kaizen doesn’t promote huge capital investments or massive changes to a process.
Instead, it focuses on using the best resource any company can have, it’s employees and encourages them to look for waste and shortcomings.
3. Increased Employee Morale
When you regularly involve employees in the process improvement process, you respect their opinions, ask for feedback and suggestions, and encourage new ideas for improvement.
This, in turn, makes employees feel valuable, gives them a sense of purpose, and hence, leads to increased employee morale and engagement.
4. Increased Efficiency
Careful observation of business processes leads to finding out waste and inefficiencies. Thus, Kaizen methodology’s main goal is to increase the overall efficiency of the process, which in turn, increases employee efficiency and provides a healthy work environment.
5. Fewer Inspections
Since Kaizen involves constant scrutiny of processes, it leads to lesser inspections and regulatory checks. This leads to a safer work environment where employees can thrive and flourish.
How to implement Kaizen at your workplace?
Now that we know the numerous benefits of Kaizen and its ability to provide gradual change without causing radical changes or heavy capital investments.
let’s see how your organization can use the power of Kaizen methodology and get on board to the path of continuous improvement.
The continuous cycle of Kaizen methodology has seven phases:
1. Educate the Employees
Remember, the implementation of Kaizen involves the collective effort of the organization and not just upper management.
Start off by educating your employees on the concept of Kaizen and how it can help them improve their work as well as life in general in a big way.
Management plays a key role in here in training the staff, explaining them the “why” behind the requirement of new changes, and encourage them to participate.
Read more: How to Create an Incredible Training Manual (Template Included)
2. Identify a Problem or Opportunity
Once employees are on board with the concept of Kaizen, take their valuable opinions on what can be done to improve an existing process or where lies new opportunities. Create a list of problems and opportunities.
3. Brainstorm Solutions
Once you know what to improve first, it’s time is to come up with a collective solution. Encourage employees to offer solutions. Use quality circles, suggestion boxes, or Kaizen boards to facilitate communication between employees and management.
4. Test the Optimal Solution
Once you decide upon the winning solution, its time to roll it out. Start with small steps and implement the solution gradually. Make sure everyone is on board and know why the particular solution was chosen to improve the process.
5. Analyze Results
Create milestones or checkpoints so as to keep tabs on whether the solution is being implemented correctly. Measure how successful the change has been and document the learnings.
6. Standardize the solution
If the results are what you hoped for, its time to standardize the solution company-wide.
One of the most important steps in the Kaizen methodology is making sure that each and every employee participates in the process improvement process.
Kaizen only works when employees at all levels of the company work together proactively to achieve incremental improvements.
The cycle of kaizen activity can also be defined as: “Plan → Do → Check → Act”. This is also known as the Shewhart cycle, Deming cycle, or PDCA cycle.
[/vc_column_text]
Image Credit: Wikipedia
Read more: Why Companies are shifting to Digital Workplaces
Advantages Of Kaizen
- Improved work efficiency
- It helps scrutinize processes so that mistakes can be minimized
- Requires teamwork
- Since mistakes are minimized, fewer resources can be spent on inspections.
- Improves employee morale
- Encourages critical thinking
Disadvantages Of Kaizen
- Training employees on a new management style can be a bit of a challenge
- It’s not easy to change people’s mindset
- If desired results are not visible, employees can get discouraged.
Over To You…
The primary goal of Kaizen is continuous improvement. As businesses continue to evolve in this digital age, change is usually brought about abruptly and that too, quite often.
Implementing Kaizen gives your organization the much-needed focus on things that actually matter and make changes at a pace everyone is comfortable with.
The most important part of implementing Kaizen is usually the development of the Kaizen mindset. The employees should be made aware of why they are doing the work they are doing and how continually looking for ways to improve can help them achieve more.
Thus, providing your teams with the proper Kaizen training, tools and the ecosystem where they can freely scrutinize wastage or errors and suggest new, creative ideas forms the foundation of change management.
As your employees become aware of the benefits of Kaizen in their personal as well as professional lives, they will likely begin taking mental ownership of their individual processes. And when this shift in mindset occurs, the employees themselves look for ways to improve their work.
Further reads:
- The Definitive Guide To Effective Workplace Communication
- Employee Training: Definition, Importance & Tools to Use!
- 12 Awesome Tips To Help You Grow Your Business!
- Happy & Collaborative Work Culture: 10 Effective Ways to Create it!
- Top 7 HR KPIs You Should Measure in 2022!
- What Is Remote Work: The Complete Guide
- How Digital Collaboration in the Workplace Improves Workflows
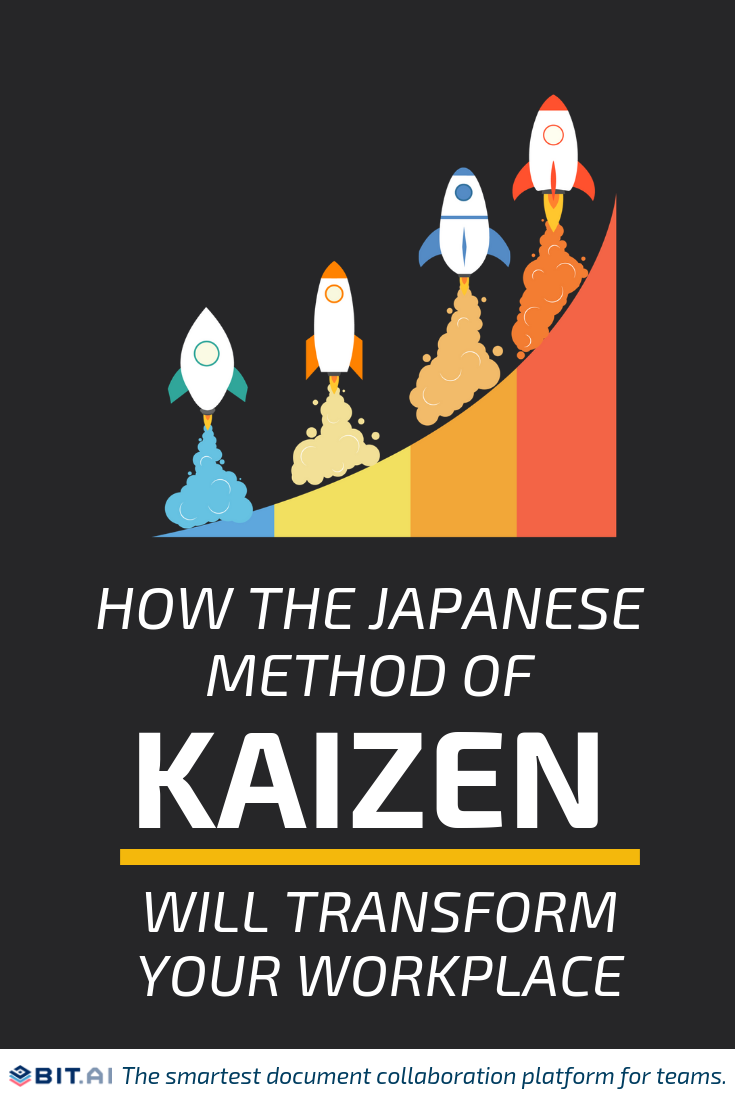