Top 20 Manufacturing Document Templates
Production and Operations
1. Production Schedule Template
A production schedule template is a vital tool in the world of manufacturing, helping you plan and manage your production activities efficiently. This template lays out the timetable for producing goods, detailing when and where each step of the production process will take place. By using this template, you can ensure that resources are allocated properly, deadlines are met, and potential bottlenecks are identified and addressed early.
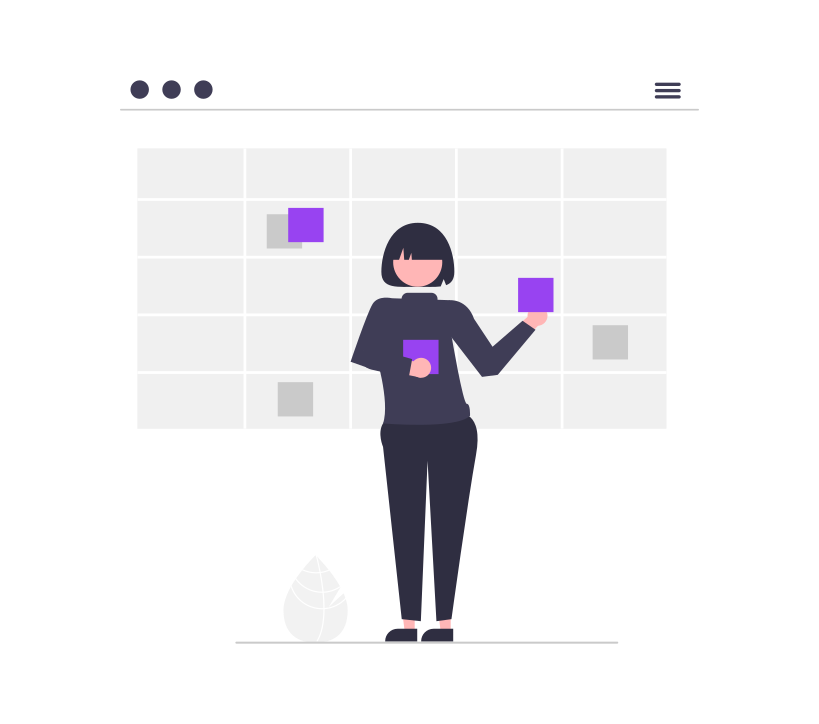
Production Tasks: List all the tasks required for production, from start to finish.
Timelines: Specify the start and end dates for each task to ensure timely completion.
Responsible Personnel: Assign team members to specific tasks to ensure accountability.
Resources Required: Note down the materials, machinery, and tools needed for each task.
Milestones: Highlight important deadlines or checkpoints within the production process.
Dependencies: Identify tasks that depend on the completion of other tasks to avoid delays.
Status Updates: Track the progress of each task to keep the schedule on course.
2. Daily Production Report Template
Here’s what you can expect to find in a daily production report template:
Date and Shift Information: Clearly specify the date and shift for the report.
Production Output: Record the number of units produced during the shift.
Downtime: Note any periods of downtime, including reasons and duration.
Quality Control: Document any quality issues or defects identified during production.
Labor Utilization: Track the number of workers on the shift and their hours worked.
Material Usage: Log the amount of raw materials used during the shift.
Maintenance Activities: Include details of any maintenance performed on equipment.
3. Work Order Template
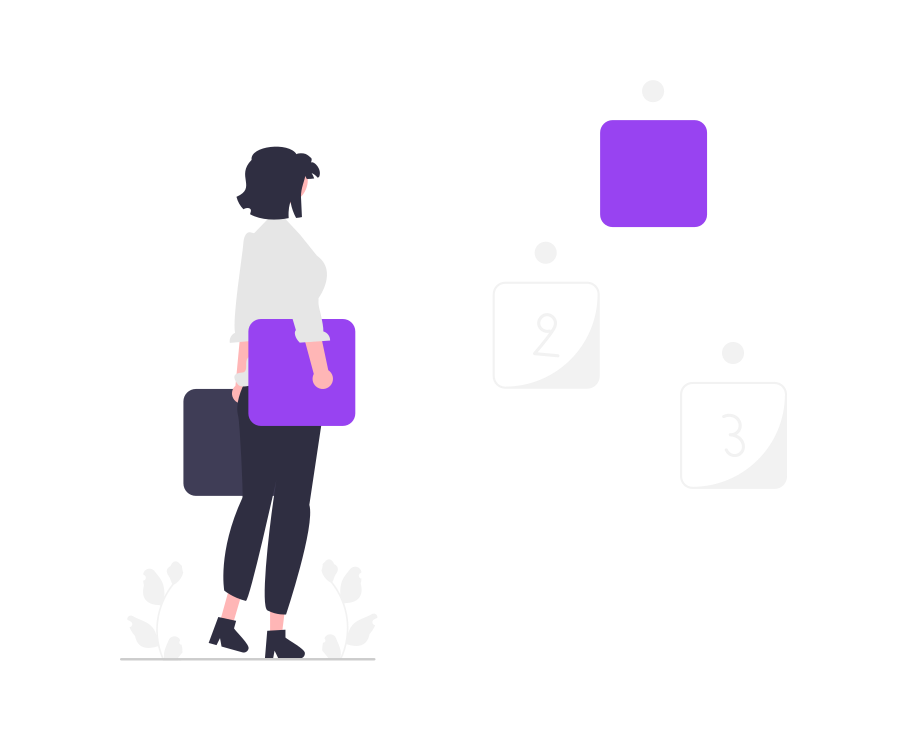
Work Order Number: Assign a unique identifier to each work order for easy tracking.
Description of Work: Provide a detailed description of the task to be completed.
Priority Level: Indicate the urgency of the work to prioritize tasks effectively.
Assigned Personnel: Name the person or team responsible for carrying out the work.
Materials and Tools Needed: List all required materials and tools for the job.
Estimated Completion Time: Give an estimated timeframe for task completion.
Approval Signatures: Include space for signatures to authorize and validate the work order.
4. Process Documentation
Process Title: Clearly state the name of the process being documented.
Objectives: Outline the goals and purpose of the process.
Scope: Define the boundaries and limitations of the process.
Responsibilities: Specify who is responsible for each part of the process.
Step-by-Step Instructions: Provide detailed, sequential steps to follow.
Materials and Equipment: List the necessary materials and equipment required.
Quality Control Measures: Describe the checks and standards to ensure quality.
Quality and Safety
5. Quality Control Checklist
Item Description: Clearly state what is being inspected.
Inspection Criteria: List the standards or specifications the item must meet.
Inspection Method: Describe how the inspection should be carried out.
Frequency of Inspection: Specify how often the inspections should occur.
Acceptance Criteria: Define what constitutes a pass or fail for each inspection point.
Inspector’s Name: Record who performed the inspection.
Comments and Observations: Provide space for notes on any findings or issues.
Sign-off Section: Include a space for the inspector to sign off once the inspection is complete.
Quality Control Checklist Example:
Product Name: ____________________________
Batch Number: ___________________________
Date of Inspection: _______________________
Inspected By: ____________________________
Inspection Point | Criteria | Method | Frequency | Result (Pass/Fail) | Comments |
Material Quality | No defects | Visual inspection | Every batch | ||
Dimensions | Within tolerance | Caliper measurement | Every 10 items | ||
Weight | Within limits | Scale measurement | Every 20 items | ||
Assembly Accuracy | Correct assembly | Visual and functional | Every item | ||
Packaging | Proper labeling | Visual inspection | Every batch |
6. Safety Incident Report Template
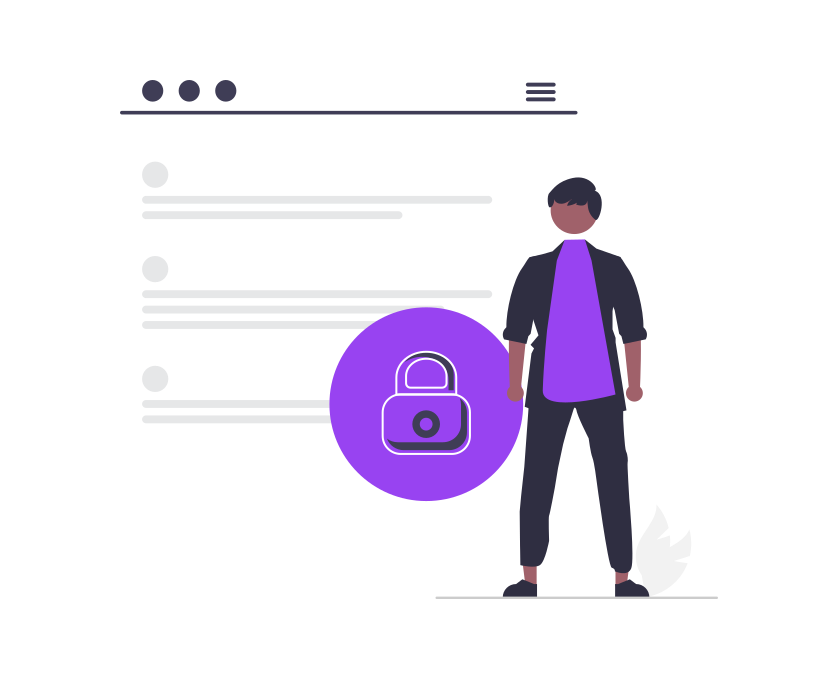
Incident Date and Time: Record the exact date and time the incident occurred.
Location: Specify where the incident took place within the facility.
Description of Incident: Provide a detailed account of what happened.
Injuries Sustained: Note any injuries, including the nature and extent.
Witnesses: List any witnesses to the incident and their contact information.
Immediate Actions Taken: Document any immediate measures taken to address the incident.
Root Cause Analysis: Identify the underlying cause of the incident.
Corrective Actions: Outline steps to prevent a recurrence of the incident.
7. Job Safety Analysis (JSA) Template
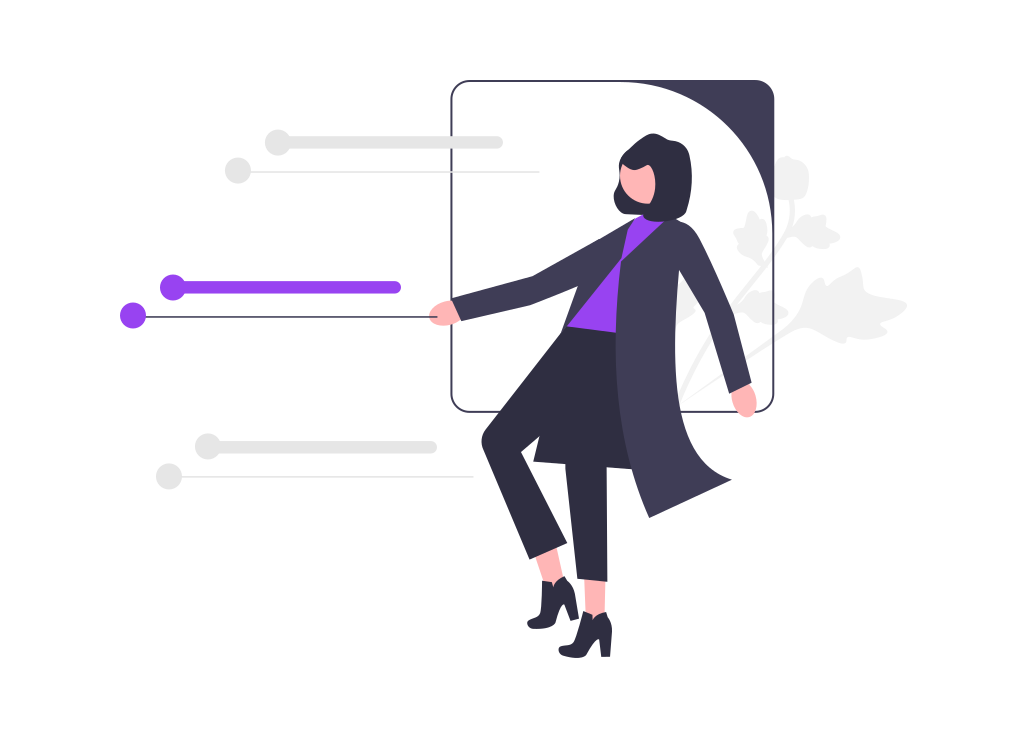
Job Title: Clearly state the job or task being analyzed.
Job Steps: List each step of the job in sequence.
Potential Hazards: Identify the hazards associated with each step.
Risk Assessment: Evaluate the severity and likelihood of each hazard.
Preventive Measures: Outline the actions to eliminate or reduce risks.
Responsible Person: Assign responsibility for implementing preventive measures.
Review Date: Include a date for reviewing and updating the JSA.
8. Compliance Checklist
Regulation Reference: Cite the specific law or standard being checked.
Checklist Items: List the specific requirements that need to be met.
Verification Method: Describe how compliance will be verified.
Frequency: Specify how often each compliance item should be checked.
Responsible Person: Assign who is responsible for ensuring compliance.
Compliance Status: Indicate whether each item is compliant or not.
Comments: Provide space for additional notes or observations.
Compliance Checklist Example:
Facility Name: ____________________________
Inspection Date: __________________________
Inspected By: ____________________________
Regulation | Requirement | Method | Frequency | Responsible | Status (Compliant/Non-compliant) | Comments |
OSHA General Duty Clause | Safe work environment | Visual inspection | Monthly | Safety Manager | ||
Environmental Regulations | Proper waste disposal | Documentation review | Quarterly | Environmental Officer | ||
Machine Safety Standards | Guarding on equipment | Equipment inspection | Weekly | Maintenance Supervisor | ||
Fire Safety Codes | Accessible fire exits | Walkthrough | Monthly | Safety Officer | ||
Employee Training Requirements | Annual safety training | Training records review | Annually | HR Manager |
Maintenance and Equipment
9. Maintenance Log Checklist
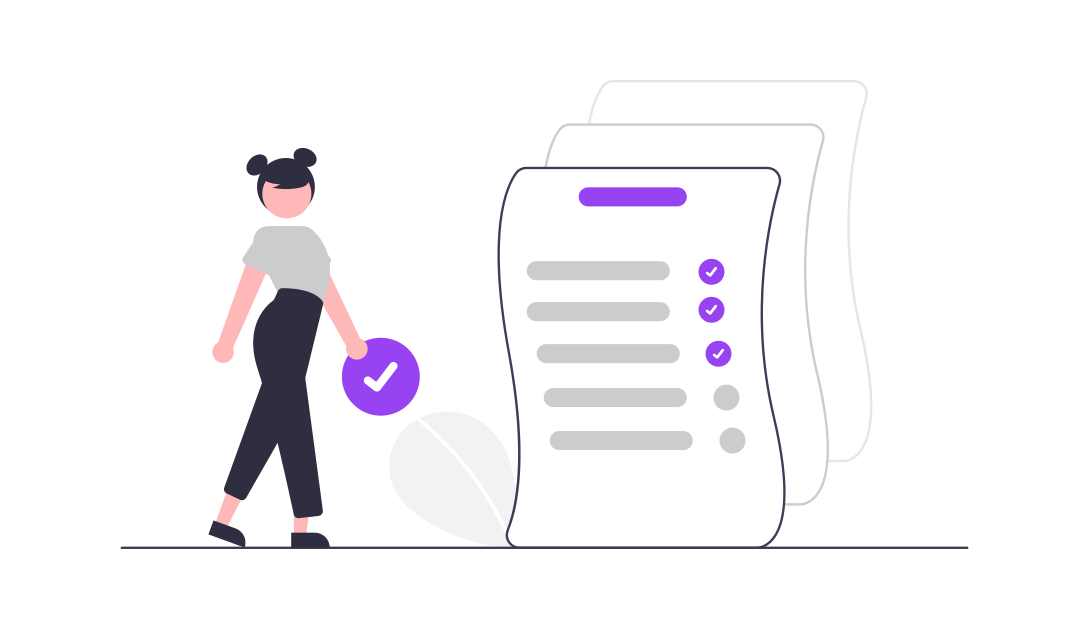
Date of Maintenance: Record the exact date when the maintenance task was performed.
Equipment ID: Specify the unique identifier for the piece of equipment being maintained.
Maintenance Description: Provide a detailed description of the maintenance work carried out.
Technician Name: Note who performed the maintenance.
Parts Replaced: List any parts that were replaced during the maintenance.
Next Scheduled Maintenance: Indicate when the next maintenance is due.
Comments: Include space for any additional notes or observations about the maintenance task.
10. Equipment Calibration Log
Calibration Date: Record the date the calibration was performed.
Equipment ID: Specify the unique identifier for the equipment being calibrated.
Calibration Standard: Note the standard or reference used for calibration.
Calibration Method: Describe the method used to perform the calibration.
Technician Name: Record who carried out the calibration.
Results: Document the results of the calibration, including any adjustments made.
Next Calibration Due: Indicate when the next calibration is scheduled.
Comments: Provide space for additional notes or observations.
11. Equipment Maintenance Record
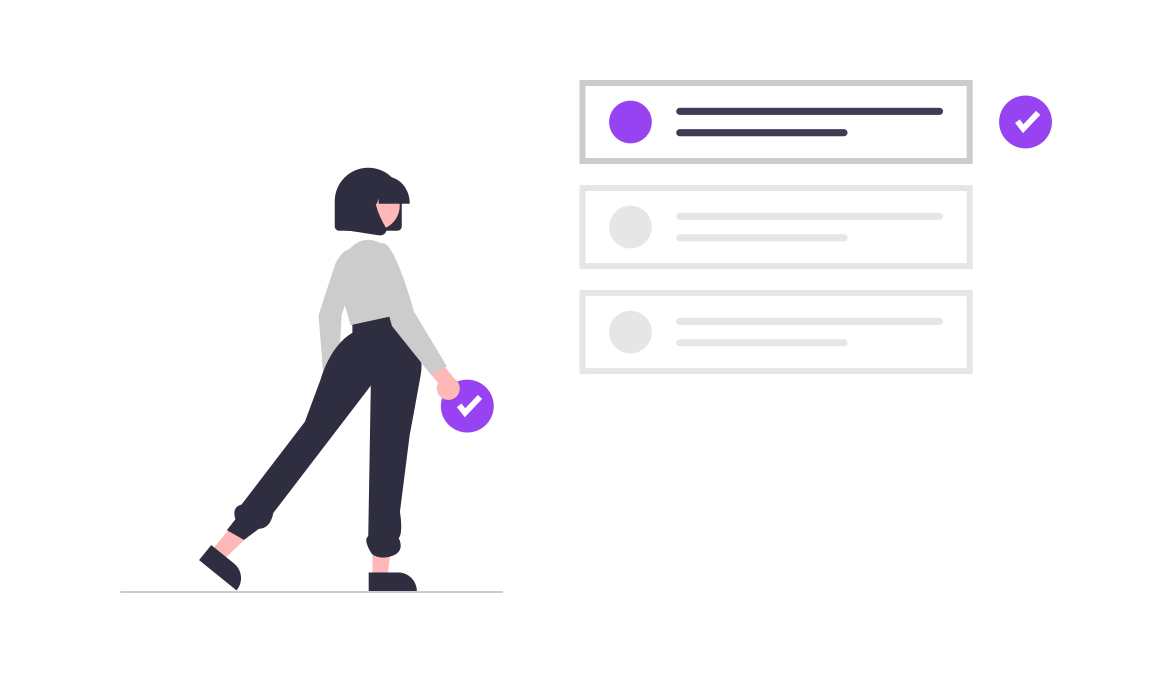
Equipment ID: Record the unique identifier for the piece of equipment.
Maintenance Date: Note the date when maintenance was performed.
Description of Work: Provide a detailed description of the maintenance work carried out.
Service Provider: Record who performed the maintenance, whether internal staff or an external service provider.
Parts Replaced: List any parts that were replaced during the maintenance.
Cost of Maintenance: Document the cost associated with the maintenance activity.
Next Scheduled Maintenance: Indicate when the next maintenance is due.
Comments: Include space for any additional notes or observations.
12. Preventive Maintenance Checklist
Task List: Detail all the specific maintenance tasks that need to be performed.
Frequency: Specify how often each task should be completed (e.g., daily, weekly, monthly).
Responsible Person: Assign who is responsible for each maintenance task.
Inspection Criteria: Describe what to look for during each inspection or maintenance task.
Tools and Materials Needed: List any tools or materials required to complete the task.
Completion Date: Record the date when each task is completed.
Comments: Provide space for additional notes or observations.
Preventive Maintenance Checklist Example:
Equipment ID: ____________________________
Date: __________________________
Maintained By: ____________________________
Task | Frequency | Responsible | Inspection Criteria | Tools Needed | Completion Date | Comments |
Lubricate moving parts | Monthly | Maintenance Technician | Check for proper lubrication | Lubricant, grease gun | ||
Inspect electrical wiring | Quarterly | Electrician | No frayed wires or loose connections | Multimeter, gloves | ||
Test safety devices | Monthly | Safety Officer | Functioning correctly | Test equipment | ||
Clean filters | Monthly | Maintenance Staff | No dust or debris | Cleaning supplies | ||
Check fluid levels | Weekly | Operator | Within safe range | Measuring tools |
Inventory and Supply Chain Management
13. Bills of Material Template
Product Name and Description: Clearly specify the product for which the BOM is created.
Part Number: Assign a unique identifier to each component or material.
Part Description: Provide a detailed description of each part or material.
Quantity Required: Indicate the quantity of each component needed for one unit of the product.
Unit of Measure: Specify the unit of measurement (e.g., pieces, kilograms).
Supplier Information: Include the name and contact details of the supplier for each part.
Cost per Unit: Record the cost of each component to calculate the total production cost.
Assembly Instructions: Offer brief instructions on how to assemble the components.
14. Inventory Management Template
Item Name: List the name of each inventory item.
Item Code: Assign a unique code to each item for easy identification.
Category: Classify items into categories (e.g., raw materials, finished goods).
Stock Level: Record the current quantity of each item in stock.
Reorder Level: Specify the minimum stock level at which an item should be reordered.
Supplier Details: Include the name and contact information of suppliers.
Unit Price: Note the cost per unit of each inventory item.
Total Value: Calculate the total value of stock on hand for each item.
Last Order Date: Record the date when the item was last ordered.
15. Supplier Evaluation Form
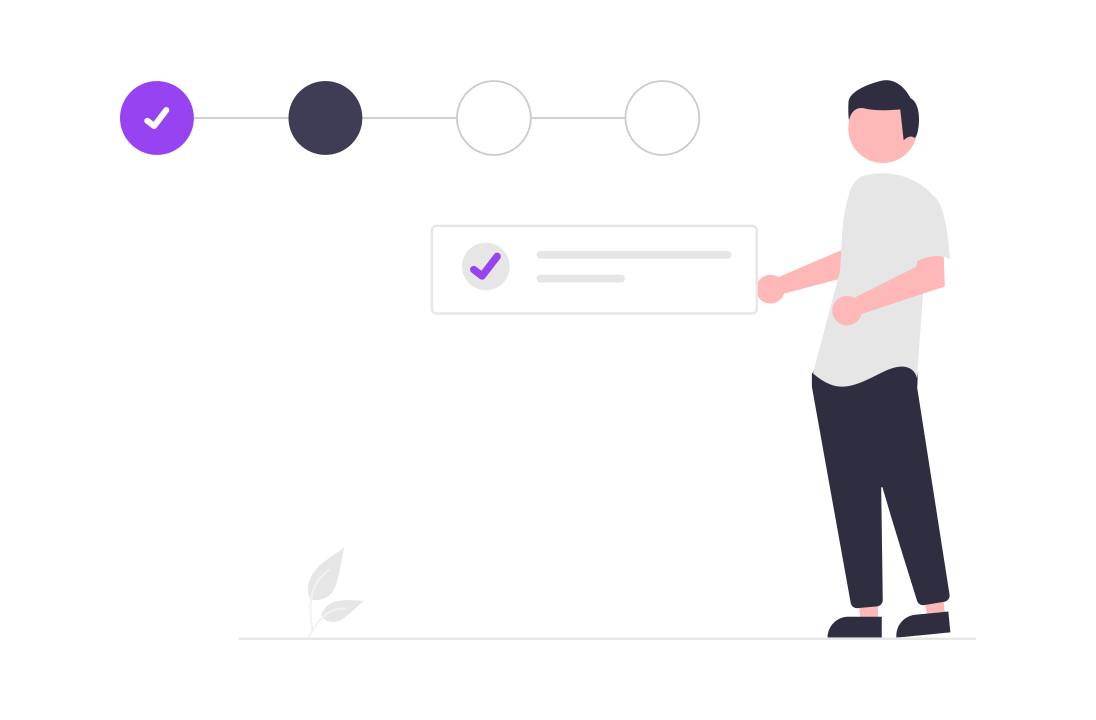
Supplier Name: Record the name of the supplier being evaluated.
Evaluation Date: Note the date when the evaluation is conducted.
Product/Service Provided: Specify the products or services supplied by the vendor.
Quality of Products: Rate the quality of the products supplied.
Delivery Performance: Evaluate the timeliness and reliability of deliveries.
Pricing: Assess the competitiveness and transparency of the supplier’s pricing.
Communication: Rate the supplier’s responsiveness and communication skills.
Compliance: Check whether the supplier complies with relevant regulations and standards.
Overall Score: Provide an overall rating based on the various evaluation criteria.
Supplier Evaluation Form Example:
Supplier Name: ____________________________
Evaluation Date: __________________________
Evaluated By: ____________________________
Criteria | Rating (1-5) | Comments |
Quality of Products | ||
Delivery Performance | ||
Pricing | ||
Communication | ||
Compliance | ||
Overall Score |
16. Vendor Management Template
Vendor Name: Record the name of each vendor.
Contact Information: Include contact details such as phone number, email, and address.
Products/Services Provided: Specify the products or services each vendor supplies.
Contract Details: Note the key terms and conditions of the contract with each vendor.
Performance Metrics: Track and evaluate the performance of each vendor based on set criteria.
Payment Terms: Document the agreed payment terms and schedules.
Order History: Maintain a record of all orders placed with each vendor.
Communication Log: Keep track of all communications with vendors, including emails and phone calls.
Project and Performance Management
17. Project Management Gantt Chart
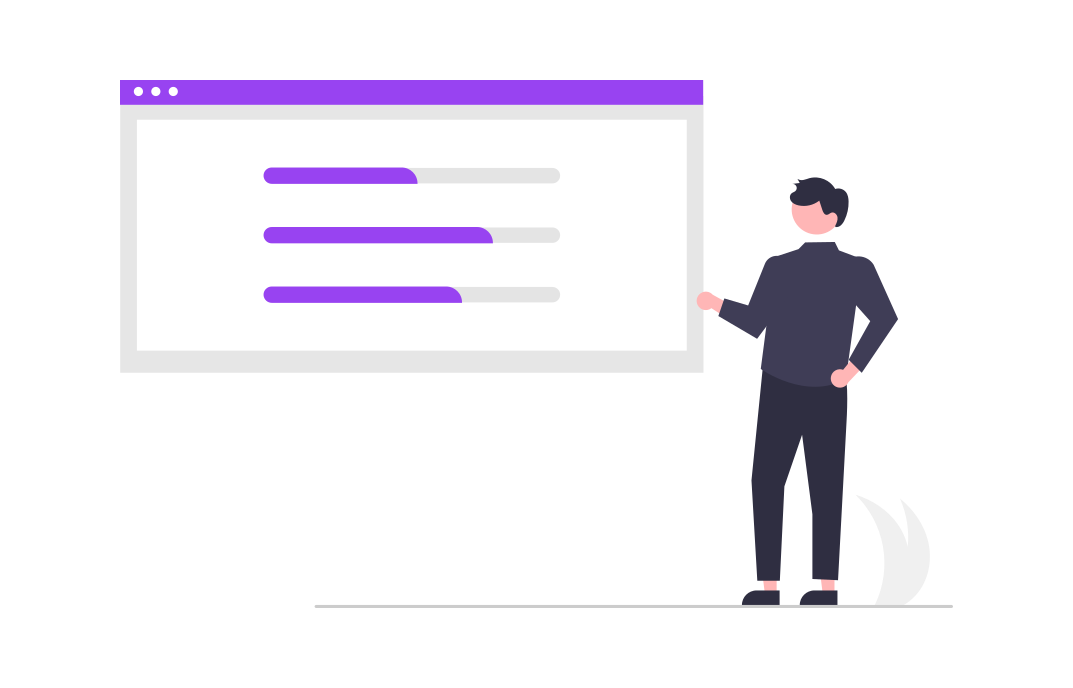
Task List: List all the tasks and activities that need to be completed.
Start Date: Indicate the starting date for each task.
End Date: Specify the expected completion date for each task.
Duration: Calculate the total time required to complete each task.
Dependencies: Identify tasks that depend on the completion of other tasks.
Progress Tracking: Use bars or other indicators to show the current progress of each task.
Assigned Resources: Note who is responsible for each task.
Milestones: Highlight key milestones or important deadlines within the project.
18. Cost Benefit Analysis Template
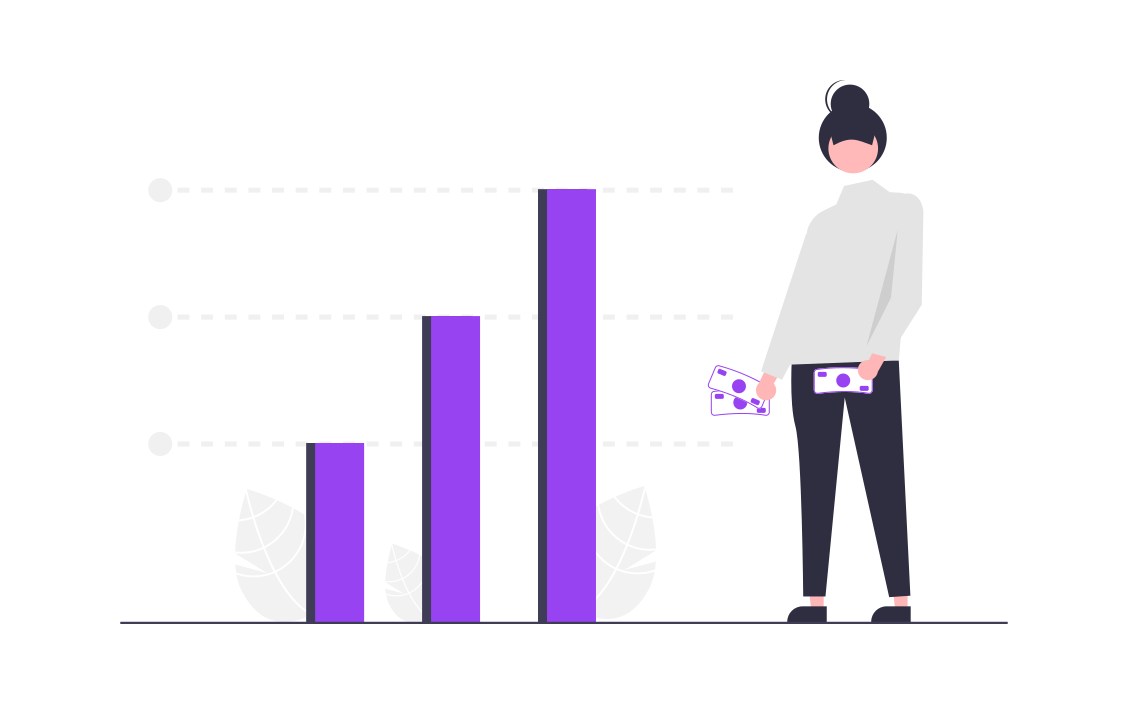
Project Description: Clearly state the project or decision being analyzed.
Costs: List all the costs associated with the project, including direct, indirect, and opportunity costs.
Benefits: Identify and quantify all the benefits the project is expected to deliver.
Timeframe: Specify the period over which the costs and benefits will be evaluated.
Net Present Value (NPV): Calculate the NPV to assess the profitability of the project.
Cost-Benefit Ratio: Determine the ratio of benefits to costs to evaluate the overall value.
Risk Assessment: Analyze potential risks and uncertainties that might impact the project.
Conclusion and Recommendations: Summarize your findings and provide recommendations based on the analysis.
19. Change Request Form
Change Request ID: Assign a unique identifier to each change request.
Request Date: Note the date when the change request is submitted.
Requestor Information: Record the name and contact details of the person requesting the change.
Change Description: Provide a detailed description of the proposed change.
Reason for Change: Explain why the change is necessary.
Impact Assessment: Evaluate the potential impact of the change on the project’s scope, schedule, and resources.
Cost Estimate: Provide an estimate of any additional costs associated with the change.
Approval Status: Include sections for approval or rejection, with signatures from relevant stakeholders.
Change Request Form Example:
Change Request ID: ____________________________
Request Date: __________________________
- Requestor Name: ____________________________
Requestor Contact: ____________________________
Change Description | |
Reason for Change | |
Impact Assessment | |
Cost Estimate | |
Approval Status | |
Approved/Rejected By | |
Date |
20. Employee Performance Review Template
- Employee Information: Record the employee’s name, job title, and department.
Review Period: Specify the timeframe covered by the review.
Performance Criteria: List the key performance indicators (KPIs) and criteria used for the evaluation.
Rating Scale: Use a consistent rating scale (e.g., 1-5) to assess performance against each criterion.
Strengths: Highlight the employee’s strengths and areas where they excel.
Areas for Improvement: Identify areas where the employee can improve.
Goals and Objectives: Set specific, measurable goals for the next review period.
Comments and Feedback: Provide space for additional comments and feedback from both the reviewer and the employee.
Reviewer’s Signature: Include a section for the reviewer’s signature and date to formalize the review.
Conclusion
Remember to always keep your documents updated, involve your team in using these templates, and customize them to fit your specific needs.
Ready to make your manufacturing smoother and more organized? Dive in and get started!
Further Reads:
Best Performance Review Tips For Managers (Template Included)
Leverage the Power of Knowledge Management to Streamline Manufacturing
Top 20 Event Management Document Templates for 2025
Study Guide: What is it & How to Create an Amazing One?
13 Types of Plans Your Business Must Have!
Related posts
Bit.ai | Watch to Learn More
What is Bit.ai?
Bit.ai is an innovative AI-driven knowledge and Document Managment suite designed to empower knowledge workers by streamlining the creation of, documents, wikis, and notes. With an intuitive interface and seamless integration, Bit.ai acts as a versatile assistant to help you collaborate, generate, organize, and visualize your ideas effortlessly. Whether you are drafting a report, managing a project, collaborating with your team or clients, or brainstorming new concepts, Bit.ai brings intelligence and creativity to every aspect of your work process.